What does MFC & MFM stand for?
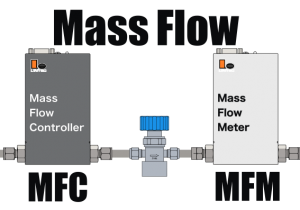
MFC & MFM stand for “mass flow controller” and “mass flow meter” respectively. They are instruments widely used in the semiconductor industry for measuring and controlling the mass flow of fluids.
What is the difference between mass flow and volumetric flow?
Mass flow and volumetric flow both express the same flow rate (the amount of flow in unit time), but volumetric flow requires consideration of density factors that vary with temperature and pressure. Mass flow, on the other hand, uses mass as the unit of measure, and thus can accurately measure flow rate without considering density.
In mass flow, the value sought is mass, or weight. It expresses the weight of material flowing per a unit of time. These units are represented by SCCM or SLM for gas measurement and g/min for liquid measurement. Volumetric flow rate, on the other hand, is the value sought in volume, or volumetric volume. It expresses the volume of material flowed per unit time. Regardless of whether it is a gas or a liquid, the general unit of volume flow is the volume at a specified temperature and pressure, such as ℓ/min.
What are the mass flow measurement units?
The units for mass flow measurement are SCCM or SLM for gases and g/min for liquids. These units represent the volume at which the instantaneous flow rate continues for one minute at 0℃ temperate and 1 ATM pressure. There are also such measurement units as NCCM, NLM, CC and LM with temperature conditions being different from the former units: 20℃ for NCCM/NLM and 25℃ for CC and LM respectively.
SCCM
SCCM stands for standard cubic centimeter per minute; in semiconductor industry, the ideal state of gas is considered to be at 0℃ temperate and 1 ATM pressure. At Lintec, it represents the volume (cc) of gas that flows for one minute at 0℃ temperate and 1 ATM pressure. Please note, that depending on industry, these standards might be different.
SLM
SLM stands for standard liter per minute, the volume (ℓ) of an instantaneous flow rate under 0℃, 1 atm equivalent conditions for one minute. It exceeds the SCCM flow rate by 1000 times. Note, however, that temperatures considered standard may differ.
NCCM
NCCM stands for normal cubic centimeter per minute, the volume (cc) of an instantaneous flow rate for 1 minute at 20℃ temperature and 1 atm pressure.
NLM
NLM stands for normal cubic centimeter per minute, the volume (ℓ) of an instantaneous flow rate for 1 minute at 20℃ temperature and 1 atm pressure. The flow rate is 1000 times higher than NCCM.
CCM
CCM stands for normal cubic centimeter per minute, the volume (cc) of an instantaneous flow rate for 1 minute at 25℃ temperature and 1 atm pressure.
LM
LM stands for normal cubic centimeter per minute, the volume (ℓ) of an instantaneous flow rate for 1 minute at 25℃ temperature and 1 atm pressure. The flow rate is 1000 times higher than CCM.
g/min
g/min stands for a unit of mass flow rate of the liquid, the volume (g)of an instantaneous flow rate for 1 minute.
What is operating differential pressure?
Operating differential pressure refers to the differential pressure between the inlet and the outlet pressures required for a mass flow controller or mass flow meter to operate properly. The internal structure of mass flow controller and meter include flow measurement section and flow restriction section, which generate a certain amount of pressure loss. Therefore, the differential pressure is required to be within the MFC specifications. Generally, the operating pressure of mass flow controllers ranges from 50 to 300 kPa. However, depending on conditions, such as low differential pressure, liquefied gas or high differential pressure, the pressure and flow rate specifications differ. Please choose the model accordingly.
What is the operating differential pressure of the mass flow controller?
Typically, mass flow controllers have operating differential pressure ranging from 50 to 300 kPa. For high flow rates, the required differential pressure tends to be higher. Additionally, if liquefied gas is controlled by using a general mass flow controller with large differential pressure, the temperature may drop due to the Joule-Thomson effect and the gas may liquefy. Therefore, for liquefied gases, it is necessary to select a mass flow controller with low differential pressure specification.
What is the control range of the mass flow controller?
Generally, control range of mass flow controllers is 2 to 100% F.S. (full scale). Therefore, if the set value is less than 2%, the control valve will be fully closed, resulting in 0% control. However, depending on the model, option, and specification, Lintec MFCs can control the set flow rate even if the set value is less than 2%. Please contact us for more information.
What is the conversion factor?
Mass flow controllers control the mass flow rate of various fluids. For thermal mass flow controllers, the heat up rate (specific heat) is different depending on the type of fluid, so it is necessary to correct it by using a fluid-specific coefficient. This coefficient is called “conversion factor”.
Typical Conversion Factors
gas type | C.F. | gas type | C.F. |
---|---|---|---|
nitrogen (N2) | 1.000 | Air | 1.000 |
Helium (He) | 1.400 | Carbon monoxide (CO) | 1.000 |
Hydrogen (H2) | 1.010 | Carbon dioxide (CO2) | 0.740 |
Oxygen (O2) | 0.990 | Nitric oxide (NO) | 0.990 |
Argon (Ar) | 1.400 | Acetylene (C2H2) | 0.630 |
Conversion Factor Measurement
Conversion factor measurement employ the build-up method of Boyle-Charles’ law.
C.F. measurement procedure by build-up method
- Evacuate the volume downstream the N2-calibrated mass flow controller.
- Shut off the valve on the secondary side of the evacuated volume.
- Mass flow controller controls the gas at set flow rate.
- Calculate the flow rate based on the pressure rise and temperature at the mass flow controller downstream volume.
- Calculate the ratio between the measured flow rate and the set N2 flow rate.
Conversion Factor Calculation
If the constant pressure specific heat and molecular weight are known, the conversion factor can be calculated. If the conversion factor is unknown, please contact Lintec directly.
Mixed gas conversion factor
Lintec MFCs can control mixed gasses. When using a mixture of two or more gases with different conversion factors, the conversion factor changes depending on the gas ratio. For such applications, please contact us directly.
What mass flow measurement methods are available?
The main methods of mass flow measurement include the following
- Thermal MFC: A method of measuring mass flow rate using specific heat of the fluid. MFC generates heat and measures the change of the temperature in the fluid, and estimates the mass from the amount of change. Generally, a heat generating resistor is used and the mass is calculated from the degree of heat taken away by the fluid.
- Coriolis MFC: A method that uses the inertia of the fluid to measure mass flow. A vibrating sensor is inserted into the fluid, and the amount of vibration changes depending on the mass of the fluid. The mass is estimated by detecting changes in this vibration. Coriolis mass flow meters are highly accurate and can be used with a wide range of fluids.
- Differential pressure MFC: A method to estimate the mass flow rate by measuring the pressure difference that occurs when fluid passes through a pipe. Normally these MFCs employ a bypass constriction or a specially shaped device to create a pressure difference that is proportional to the velocity of the flowing fluid. The mass flow rate is calculated based on this pressure difference. Orifice plates, venturi meters, and pitot tubes are examples of differential pressure generating parts for mass flow meters.
Each of these methods has its own characteristics and advantages, and is selected depending on the purpose of use and the properties of the fluid. It is important to select the optimal method depending on detailed performance requirements and applications.